Pipes – Cutting To Length, Deburring, Bending
The pipes should be cut to length using professional pipe cutters which are suitable for the material in use. Alternatively, fine-tooth hacksaws or suitable electric saws may be used. The cut has to be perpendicular to avoid negative impact on the mechanical resistance between fitting and pipe.
Only use suitable tools that are suitable for the material to be processed. Particular attention must be paid for example, to the choice of the right saw blades or cutting wheels that are used.
The cutting and deburring tools must be clean, free from adherence or chips. After cutting / deburring, the cutting edges or pipe ends must be cleaned or freed from chips or impurities
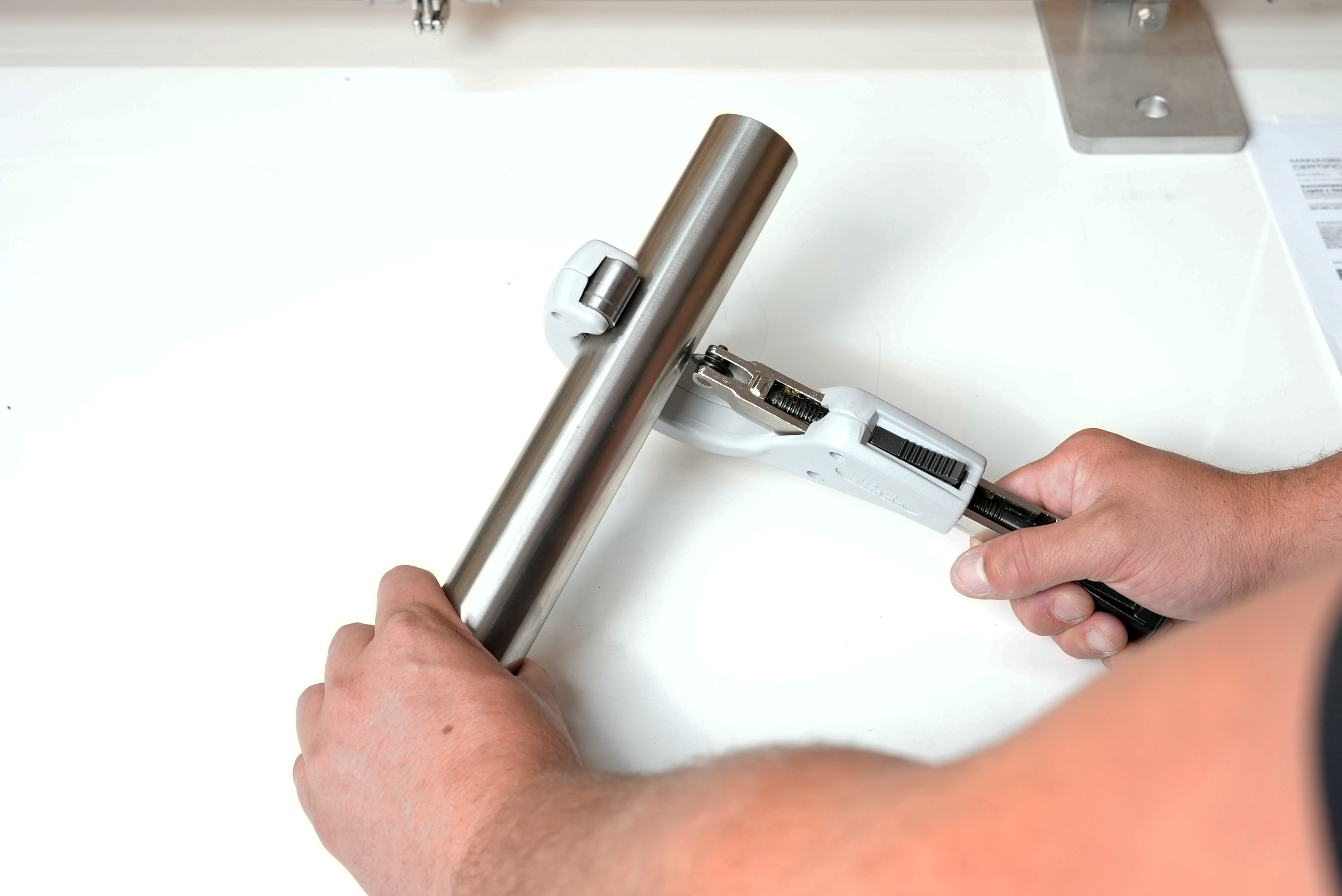
Cutting the pipe to length
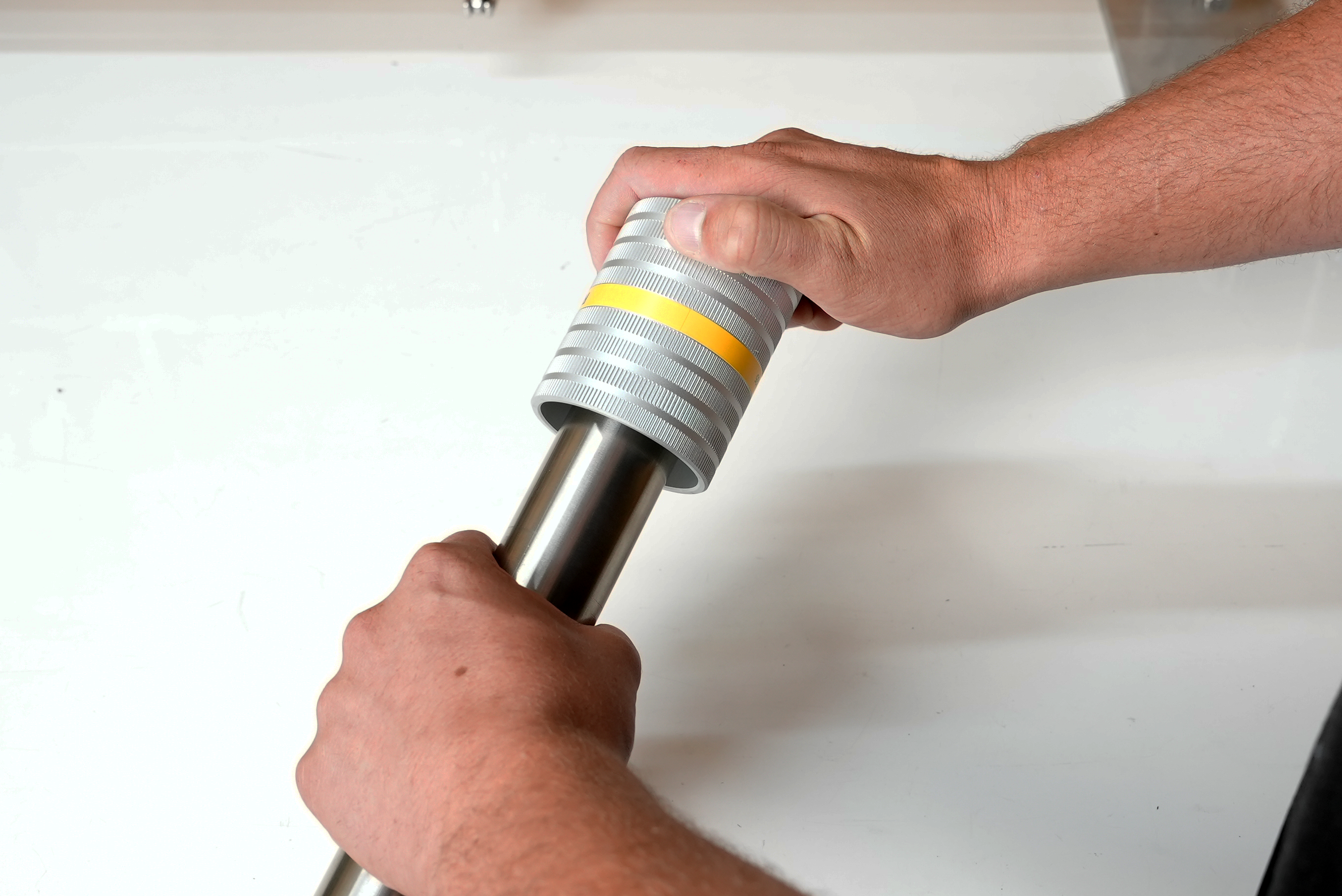
Deburring the tube
Marking The Insertion Depth / Stripping
Sufficient mechanical strength of the press fit connection will only be achieved if the insertion depths shown in table 13 are adhered to. These insertion depths are valid for pipes or fittings with insertion ends (i.e. fittings without press fit end) and must be marked using a suitable marking tool. The marking of the insertion depth on the pipe must be visible directly next to the press fit formed end following pressing. The distance of the fitting from the press fit formed end may not exceed 10% of the required insertion depth, since otherwise the mechanical stability of the connection cannot be guaranteed.
In the case of Carbon Steel PP-coated pipes the insertion depth is defined through the stripping of the plastic coating using a suitable stripping tool.
When stripping the PP-sheathed tubes, use suitable tools which do not damage the raw surface.
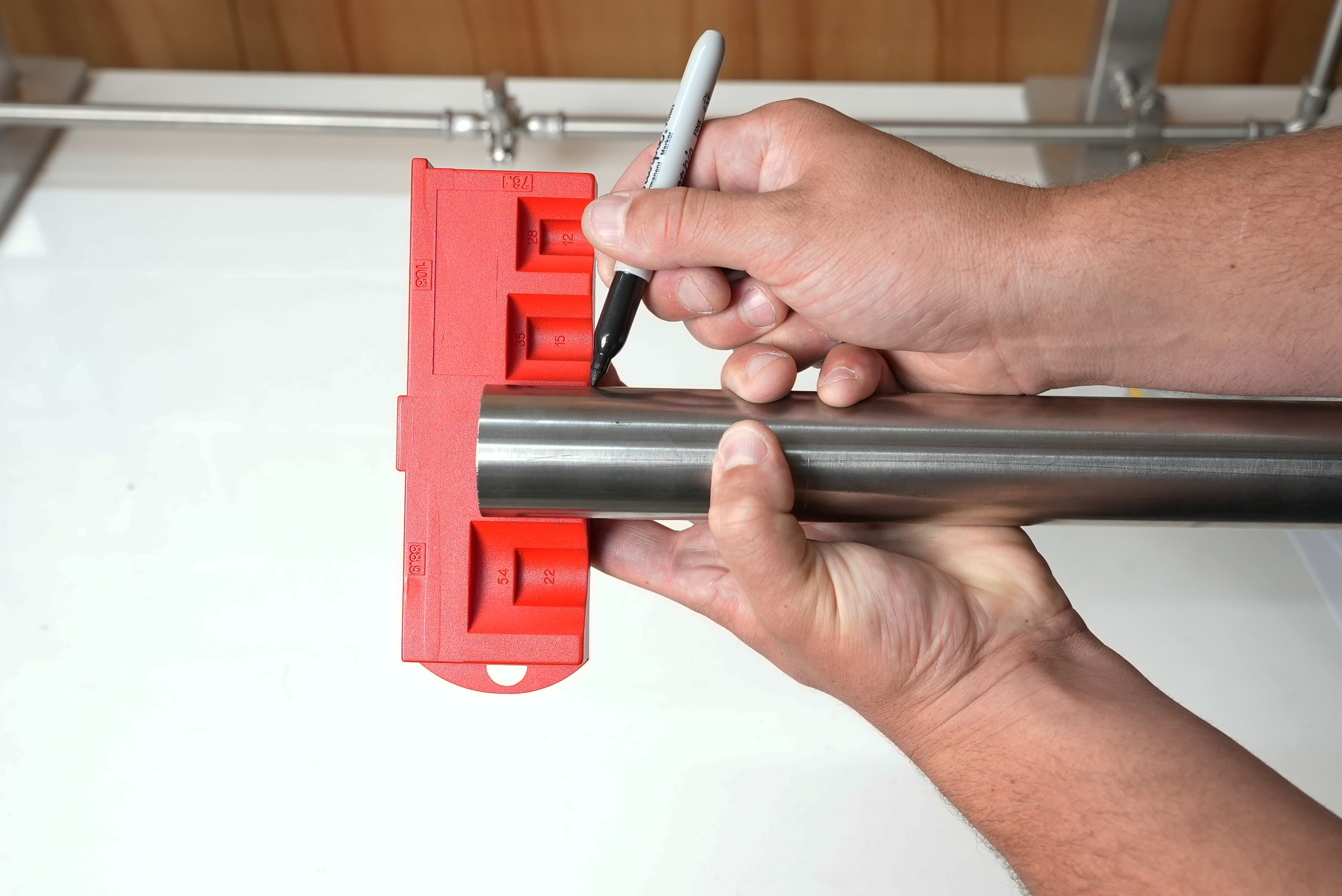
Marking the insertion depth
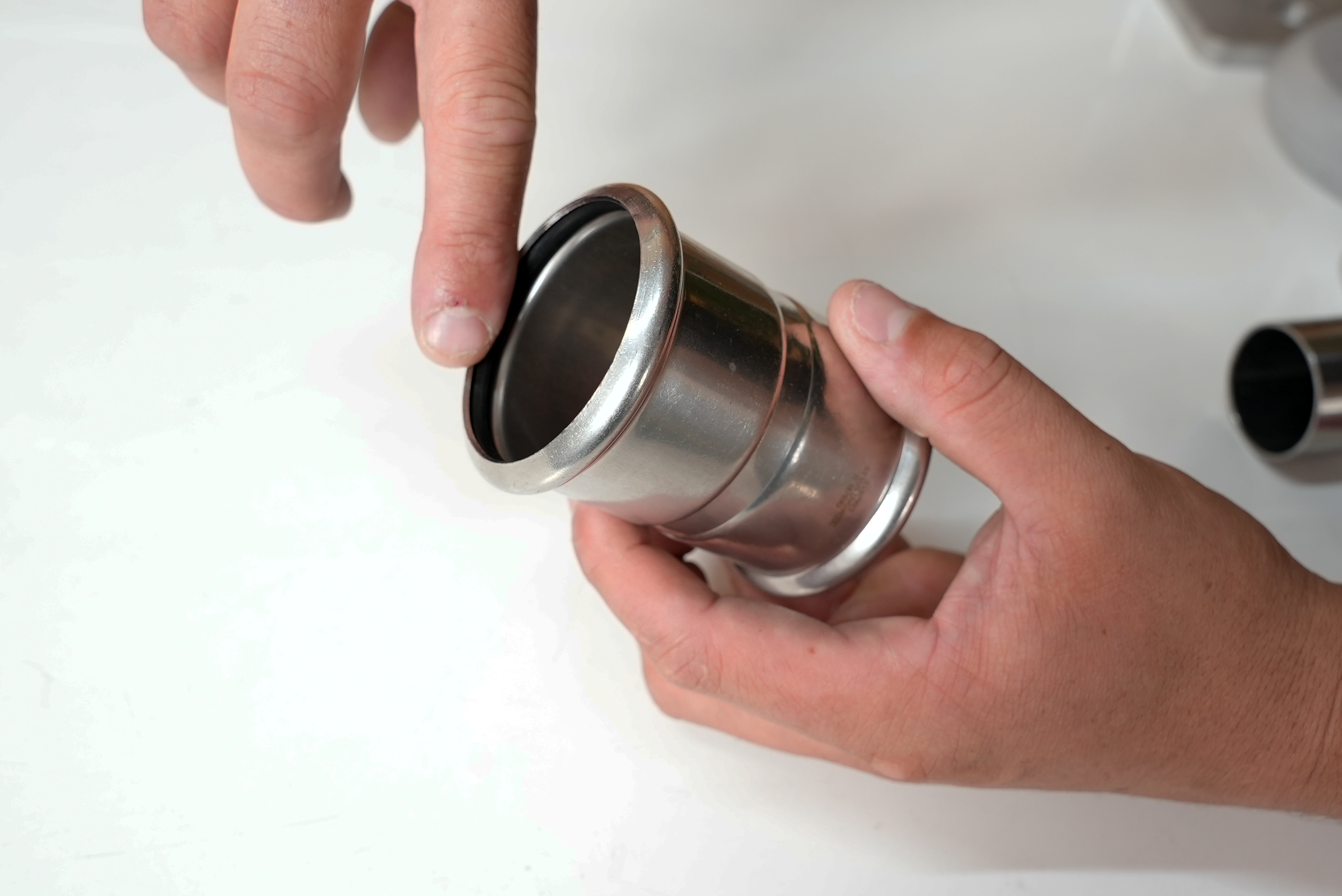
Checking the sealing ring
Press Fit Seal Ring Check
Before assembling the fittings, it is advisable to check that the sealing ring is correctly inserted in its seat and that it is not dirty or damaged. If necessary, it must be replaced.
Additionally, the fitter should check whether the ring in position is suitable for the special application, or whether another sealing ring needs fitting
Stainless Steel Oversize Range ø 139-168 mm
Unlike diameters up to 108 mm the pressing phases of the Oversize 139.7 and 168.3 mm dimensions must be carried out in two distinct pressing phases.
1st Pressing Phase
1. Open the chain and place it around the fitting:
the groove of the chain must be positioned
exactly above the toroidal chamber of the
fitting.
2. Close the chain and press the lock button.
3. Rotate the latch inwards and engage the lock.
4. Carry out pressing operation 1.
5. Unhook and rotate the latch, open the chain
and remove it from the fitting.
2nd Pressing Phase
1. Position the chain around the pipe socket
aligning it with the appropriate guides above
the containment groove of the O-ring.
2. Close the chain and press the lock button.
3. Rotate the latch inwards and engage the
lock.
4. Carry out pressing operation 2.
5. Unhook and rotate the latch, open the chain
and remove it from the fitting.
After pressing, the connection must be checked to ensure that the work has been carried out correctly and that the insertion depth is correct.
The fitter must also ensure that all connections have been adequately pressed. Once pressing has been complete, the connections must not be subjected to further mechanical loads. The alignment of the pipeline and the fixing of the threaded connections must therefore be carried out before pressing. Slight movement and lifting of pipes, E.g. for painting work is permitted.